RDAC (Remote Data Acquisition Computer)


The RDAC XF Engine monitoring module
The RDAC XF is the Engine monitor module used with Xtreme, Ultra, Enigma, Odyssey, Voyager and all iEFIS instruments.
Available in two versions, the RDAC XF is the base version and the RDAC XF MAP adds a precise silicon manifold pressure sender (usuable for any pressure in the 0 to 2.5 Bar (30psi) range (non aggressive gases or liquids only).
The RDAC XF provides an optically isolated communications interface compatible with all existing MGL EFIS systems. In addition it provides a CAN bus interface used with iEFIS systems. Further to this a RS232 interface is provided allowing thrid party (OEM) use of the RDAC system.
The RDAC XF provides up to 12 channels for thermocouple sensors (EGT,CHT), channels dedicated to NTC temperature and other probe types, oil and fuel pressure, fuel levels, dual fuel flow and dual RPM, manifold or boost pressure (RDAC XF MAP only)
The RDAC XF is quick and easy to install thanks to our well proven use of vibration proof moving cage wire terminals. These terminals allow quick attachement of wires and are very useful during typical sensor fault finding.
The RDAC XF replaces the long running RDAC XB, XD and XE versions with a more flexible, yet sturdy design in a strong, cast aluminium bulkhead mount device.
Downloadable manuals:
RDAC XF installation manual (1.6 MBytes)
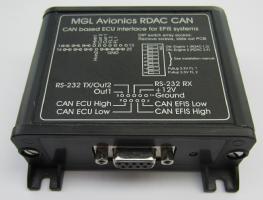
The RDAC CAN Engine monitoring module for the Rotax 912 iS
The RDAC CAN module can be used with Odyssey/Voyager G2 EFIS systems, the XTreme EFIS and EMS as well as all iEFIS systems.
The RDAC CAN module connects to the EFIS CAN bus and the CAN bus of an engine ECU system.
The first model release caters for the Rotax 912iS engine which has two ECU systems and uses the CAN Aerospace data format.
The RDAC CAN connects to both data lanes of the Rotax 912iS (ECU A and ECU B) and continues to provide engine data from lane B in case of a lane A data failure depending on user selection of the DIP switches.
The RDAC CAN can be configured as “lane exclusive” – in this mode it can be fixed to a particular lane of the Rotax 912iS. The RDAC CAN emulates RDAC 1 (Lane A) and RDAC 2 (lane B). For twin engined applications, RDACs 3 and 4 can be emulated in similar fashion.
The RDAC CAN further provides two fuel level sender inputs, one fuel pressure sender input and a current sensor input.
The fuel level sender inputs are compatible with resistive fuel senders but can also be used with any fuel level sender that can provide a DC output in the 0-3V range (internal pull-up resistors used for the resistive level senders can be switched off).
The current sensor input provides for a system that provides a zero current voltage of 2.5V with a range of 2.5V above/below this value.
The fuel pressure sender input accepts a 0-5V or 0.5-4.5V sender input range such as the popular senders available from UMA.
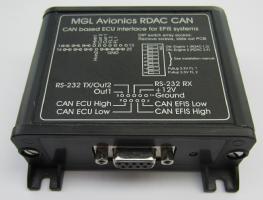
The RDAC CAN Engine monitoring module
The RDAC CAN module can be used with Odyssey/Voyager G2 EFIS systems, the XTreme EFIS and EMS as well as all iEFIS systems.
The RDAC CAN module connects to the EFIS CAN bus and the CAN bus of an engine ECU system.
This model caters for the MW B22 engine which provides information via a CAN interface.
From the engines ECU the following information is available:
- RPM
- Oil temperature
- Fuel pressure
- Manifold pressure
Further to the above the interface povides its own monitoring for:
- 2 x NTC temperature senders as fitted to the MW engine for water temperature monitoring.
- 1 x Oil pressure sender input for the MW oil pressure sender.
- 2 x Fuel level sender inputs (resistive or voltage output (0-3.3V)).
- 1 x Fuel flow input (accepts flow senders or can be used to derive flow from injector monitoring.
- 1 x Electrical current sensor (DC type centered at 2.5V such as the MGL magnetic current sender).